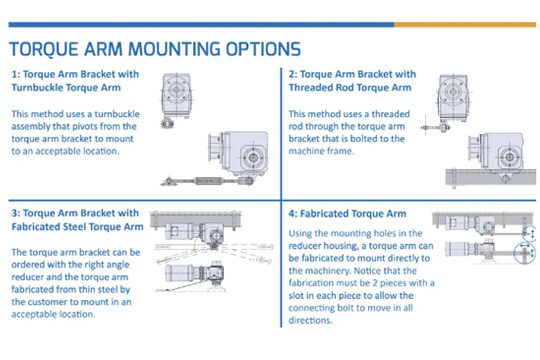
Gear reducers are often rigid mounted during installation, which can cause premature failure due to shaft runout. Rigid mounting the units puts stress on the gearing, output bearings, and seals. Since the shaft isn’t truly aligned to the gearbox, it creates radial loads on both the conveyor and the reducer bearing.
This pressure can cause the bearings to fail. In the worst case, it can fracture or break the conveyor shaft as many shafts are not within tolerance. If the gearbox cannot move with the shaft, it will stress the components and cause premature failure.
STOBER eliminates gearing misalignment, preventing premature failure through free installation training and a variety of torque arm mounting options. Torque arm mounting allows the gearbox to float on the shaft. This method reduces bearing and shaft fatigue, transmits the torque effectively, and eliminates premature failure.
STOBER offers onsite installation training for your entire maintenance team and we’re available 24 hours a day, seven days a week for any questions that might come up. With an average meantime to failure of over 9.1 years in harsh washdown applications, we know how to make gear reducers that last and want to ensure that you’re getting the most out of your STOBER products.
Want to learn more about rigid mounting failure and how to eliminate it? Download our free guide to find out how STOBER has helped a customer overcome rigid mounting below.