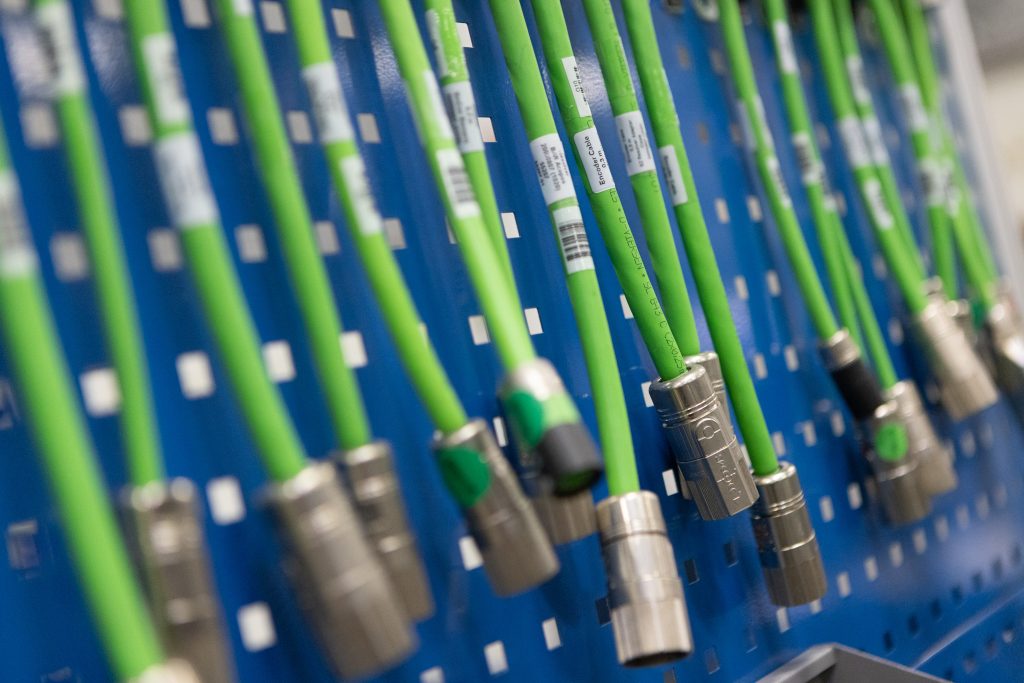
When it comes to installing and connecting cables in a manufacturing environment, It’s important to follow best practices to not only ensure safe operation, but also protect the longevity of the equipment.
Below are some recommended best practices to follow when selecting or installing cables:
- Nominal vs. peak operating voltage
Nominal voltage of the system should never be more than 1.5 times the nominal voltage of the cable. The operating voltage of a system can be 10% continuously higher than the nominal voltage of the system. This excess voltage can cause many issues, including fire, insulation degradation, and breakage of the encoder, machine, product, motor, or gearbox. - Nominal vs. peak operating current
The current-carrying capacity of the cable should not be less than the maximum current passed through the conductor under normal conditions. The allowable service temperature and flow (continuous or temporary) should also be taken into consideration, and cables should always be sized to the maximum current. - Minimum bend radius
The minimum bend radius is the smallest allowed radius the cable is allowed to be bent around. In standard operation, if the cable is flexing, elevated stress due to tension, pressure, abraision, torsion, or knicking must be avoided.- Environment
Environmental considerations can have impacts. on cables. For example, most cables have a reference point of 30 degrees Celsius ambient temperature and cannot be in direct contact with hot surfaces exceeding the thermal limit. In addition, cables are not suitable for underground laying (directly) or under carpets/devices not intended for that purpose specifically. Cable storage conditions and lifetime (including getting brittle with age) should be monitored in addition to chemical interaction, humidity, air circulation, etc.
- Environment
- Open-air condition vs. others
At STOBER, we provide cable recommendations based on the assumption of open-air condition. If cables are going to be used in conduit, with other cables, under heat or solar radiation, air circulation, or other factors, please let us know so we can adjust our recommendation. - Insulation
Heat induced either on the cable or by the cable must be appropriately managed in standard operation. - Termination and fixing
The weight of the cable can damage the connection to the terminals of the motor and/or drive without appropriate fixing. Fixing/strain relief must not damage the cable.
Strain relief is necessary–even more so when laying cables vertically. Cables should be as short as possible for the application’s needs because coiling can cause noise/heat interference. Correct termination (both in terms of quality of connection and connection location/pinout verification) Is important, and it’s especially important to know that the colors of the wire are not standardized and can vary from cable to cable.
At STOBER, we are happy to make cable recommendations for your application. Contact us today to see how we can help you find the optimal solution for your application and the communication protocol of your choice.